Cutting metal by hand can take a lot of time. When metal is being cut to make machinery or equipment, you need something that’s faster than the human hand. Electrical discharge machining is one way that people cut metal quickly. It involves using electricity to cut metal, similar to a plasma cutter, except it is underwater.
Electrical discharge machining is a very efficient way of cutting metal, especially large quantities of it. In this article, you will find six tips that will explain what electrical discharge machining is, and help you to understand it a little more:
What Is Electrical Discharge Machining?
Electrical discharge machining, or EDM, uses electricity to cut metal. Like laser cutting and other similar processes, EDM does not use mechanical force in the cutting process. This is because electricity is used instead. EDM is particularly popular in the production and manufacturing of tools, due to its ability to work with hard materials, like titanium. In addition, EDM can forge complex shapes that are hard to produce when milling. Milling is when rotary cutters are used to remove material. While milling does produce reliable cuts, EDM is a much better option.
How Does It Work?
Electrical discharge machining uses electrodes to remove material from conductive materials. Just like when you push a mould into clay, electrodes leave a negative imprint in the metal inserted into the machine’s tray. A discharge occurs in the small gaps between the metal and electrode. This discharge removes materials through vaporization or melting. In order for this to work, the metal and electrode have to be submerged in dielectric fluid. The fluid causes the discharge to become very hot, melting away the metal. The fluid is also useful for cooling the machine, during the machining process. It also controls the sparks. The number of spars produced during the EDM process is huge. If the sparks weren’t controlled, machine handlers would be in danger of being burned.
When properly controlled, electric sparks can erode and eliminate material. During the EDM process, the metal and electrode do not touch. The entire process takes place in an almost imperceptible gap. To begin, the electrode is lowered closer to the metal until the “spark gap” is achieved, and breakdown begins. The material removed by each spark is minuscule, but sparks occur over 100,000 times a second.
Types of Electrical Discharge Machining
There are three different types of EDM: wire EDM, hole drilling EDM, and die-sinking EDM. Each has its advantages. Wire EDM is by far the most effective, with the Robocut wire EDM machine being a popular choice among business owners. Here is some more information about the three different types of electrical discharge machining:
Die Sinking EDM
Die sinking uses electrodes made from copper or graphite that are pre-machined in order to have a specific shape. These electrodes are then applied to a sheet of metal, in order to create the desired shape. Die sinking is a very effective way of producing complex shapes.
Wire EDM
Wire EDM, as mentioned earlier, is perhaps the most popular and common type of EDM. Wire EDM is also called wire erosion, spark EDM, and wire burning. Wire EDM involves the use of a thin wire, which cuts the metal. Instead of having an electrode, the wire works as the electrode. Wire EDM is used to cut the outside of a piece of metal. If the middle needs to be cut, then a small hole drilling EDM will be applied to make a hole, through which the wire will then be threaded and used. Wires used in wire burning are typically made from copper and are submerged into deionized water.
Hole Drilling EDM
Hole drilling EDM is another popular and effective type of electrical discharge machining. It involves the use of a drill, as the name suggests. EDM drilling allows machine operators to drill extremely small holes, which is not usually possible with traditional drilling. The electrodes used in hole drilling EDM are tubular, and the dielectric fluid is fed through the drill. Hole drilling EDM is used for lots of different applications, including preparing metals for wire burning, as mentioned previously.
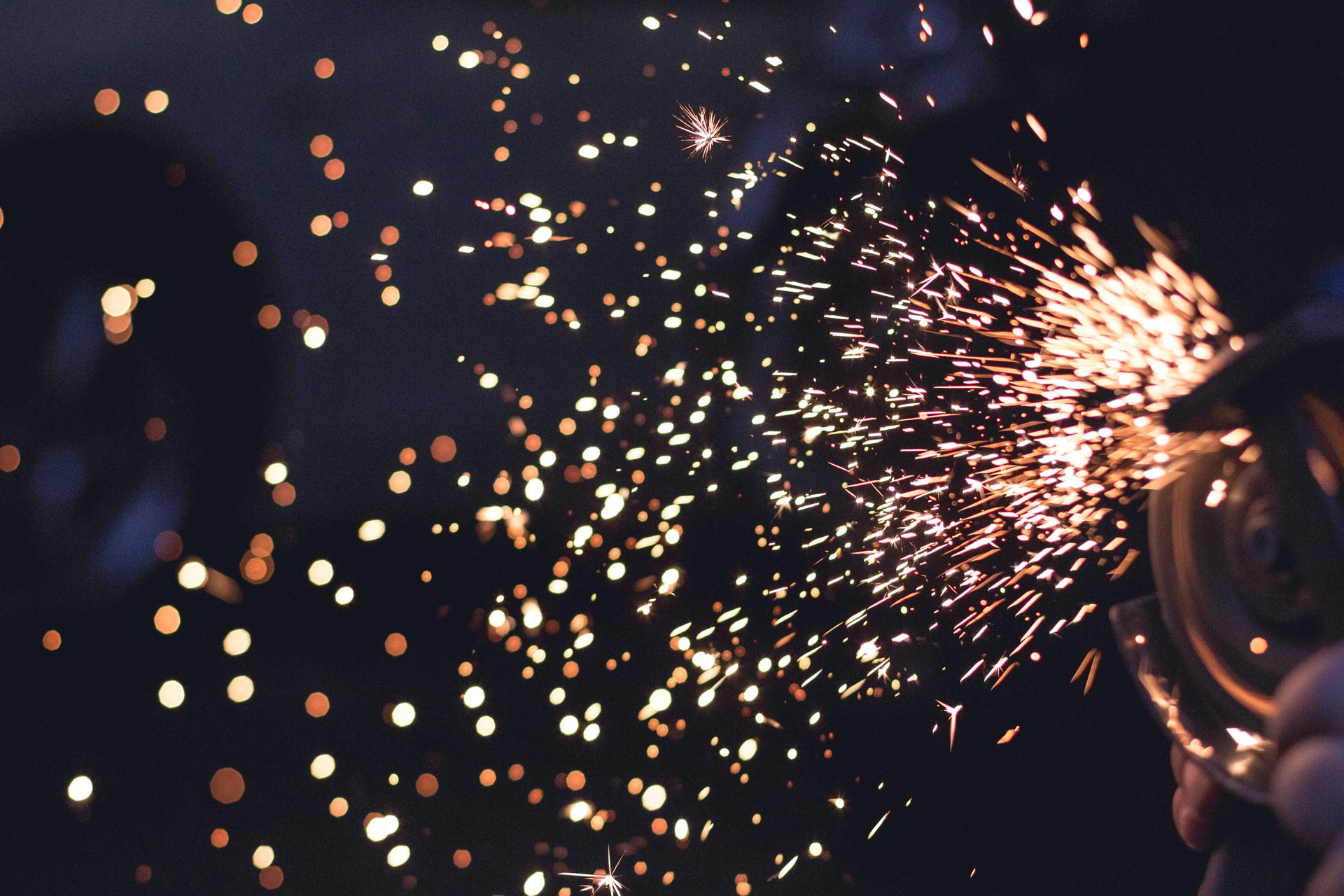
Advantages of EDM
There are far more advantages of EDM than there are disadvantages. Some of these advantages include:
- EDM allows for the production of complex shapes, that would be very difficult to produce otherwise, with traditional cutting tools.
- EDM also allows for extremely hard, tough materials to be cut. These cuts can be very detailed as well, which is not possible with a traditional cutting tool.
- In addition to being used for very large pieces of metal, EDM can be used for very small pieces, where traditional tools would cause damage.
- Weak pieces and materials can be manufactured because there is no physical contact between the electrode and the metal.
- EDM drilling does not need deburring, and no polishing is required after the process has been completed.
EDM Safety
Because of the use of electricity, handlers are often concerned about the safety of electrical discharge machining. Despite electrical involvement, EDM is actually very safe, provided that the people operating the machines have been trained properly, and proper fire measures have been installed. In addition, operators need to monitor the dielectric fluid levels. If the liquid has run out, the discharge can cross to other conductive materials. Ventilation is also required because EDM can produce gasses.
EDM Automation
At the moment, EDM machine producers are focusing on total automation. Automation eliminates the need for machine handlers and can actually make the entire process much safer. Often, injuries are caused by the machine handlers, and not the machines. Automation is something that’s becoming very relevant in today’s age, with a large focus being put on AI in the public sphere. If you are considering investing in an EDM machine, automation is something to consider. If you have the right machine, the entire process can be handled automatically.
Electrical discharge machining is becoming the preferred method of machine-cutting. It’s not hard to see why considering its long list of advantages. With the advent of automated machines, it’s clear that manual workers will no longer be needed, therefore saving companies lots of money, and a lot of time.